Manufacturing Process
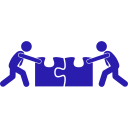
TRANS VALVES (INDIA) PRIVATE LIMITED, was incorporated in 1984 and is an ISO 9001:2015 certified company. Being a leading manufacturer of LPG Valves, Regulators and a host of other LPG Equipments as per Indian and International specifications, the company is recognized as a pioneer in the LPG Equipment Industry. We are a part of a well-diversified conglomerate having 5 state-of-the-art manufacturing units in HYDERABAD, DELHI, GHAZIABAD& RUDRAPUR for various product lines.
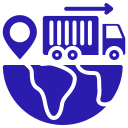
We are also a leading Export House. Our success is solely due to the unparalleled dedication and commitment of the entire team towards continuous improvement in the process and strict adherence to quality standards in producing these products.We have been actively involved with the technical development of all these products and have therefore been active members of ME 16, the Bureau of Indian Standards Technical Committee for Gas Cylinders. We are also active Panel Members in the Indian representation in ISO/TC56/SC2 the Technical Committee for Gas Cylinder Valves and Fittings. We are equipped have one of the best Test Laboratory for the testing of our products with the state of the art equipment.
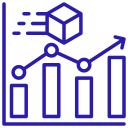
Since 1984 more than 60 million units (6 CRORE) of LPG Regulators, Valves, Adopters and other related Equipments have been sold under our brands TVL, HAPPY SING, SMARTSAFE& GASCHECK in Indian & also to the extremely stringent markets of EUROPE, USA, AFRICA, MIDDLE EAST & SAARC countries. Many of our products are certified by BIS, SGS, TUV, CE, UL, SASO. Trans Valves has gained a reputation and built an identity for quality, reliability and safety.
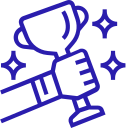
Trans Valves which holds many Patents, is also into the development of different Electronic Equipments like the LPG Gas Level Indicating Systems with various functions & features. We have also developed the Gas Leak Detection Systems for LPG. With our strong R&D base, we have the capability to undertake new, customized and innovative products & that makes us confident in delivering eco-friendly and user friendly products at most competitive prices. We are the First Company in the World to get the Approval and certification under the Saudi Arabian Standards Organization. We have been rated one amongst the best LPG Equipment Manufacturers in the World by Total Gaz.
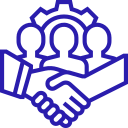
Trans Valves achieved all this through the constant efforts put-in by the dedicated team of Managers, Professionals, Skilled Engineers, Technicians and workers. The company considers its manpower resources as one of the foremost assets which are made possible by systematic training and development programs.
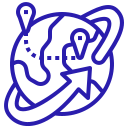
TVL has global penetration for its state of the art commercial kitchen equipments range comprising of various products for Domestic & High Pressure segments.
Yes, we at TVL believe in VALUE ENGINEERING THROUGH QUALITY & the sale of 60 million units to satisfied customers all over the world for more than 3 decades, is itself a testimony of our capability, dedication and commitment.
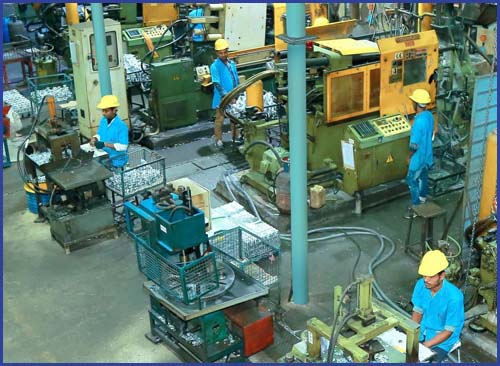
RAW MATERIAL PROCESSING
(HOT FORGING / DIECASTING)
The Raw Material is first Inspected for quality as per the standards and then taken for the processing.
For the Valves, Brass Rod is cut into desired size of billets on an automatic cutting machine. These billets and then fed through a conveyer to the Automatic Hot Forging Machine where the required type of valve is hot forged to the desired shape. They are then then left for cooling. This cooled material is sent for further process.
For the Regulators, Zinc alloy ingots are fed to the automatic Pressure Die-casting Machine. The hot molten material is automatically injected into the pressure die casting moulds to take the shape of the desired regulators. The machines cast the regulator in 2 parts called the Body & the cover (known as regulator parts). The automatic die casting machine processes the material and gives the desired moulded parts for further processing.
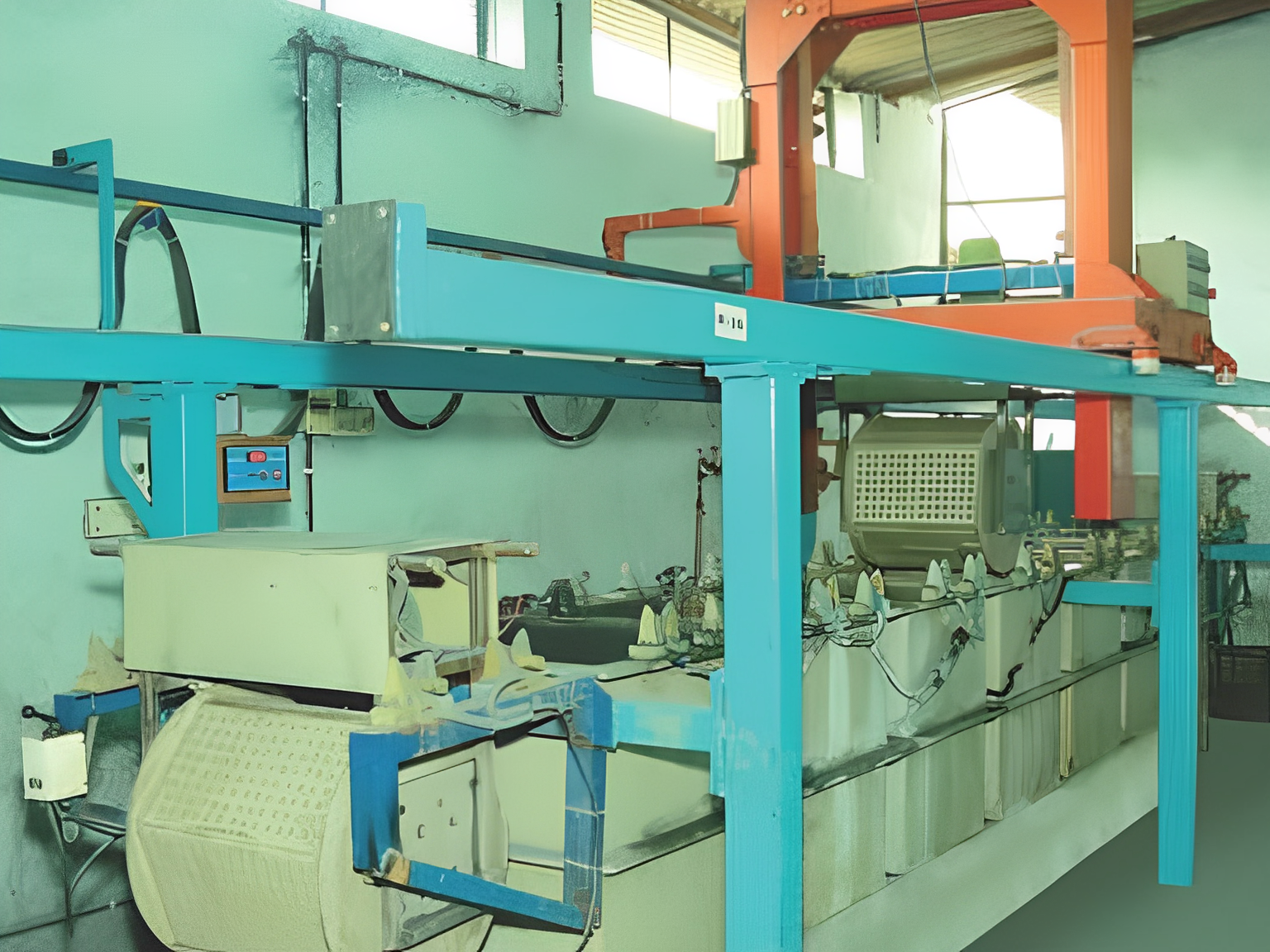
TRIMMING & SURFACE TREATMENT
The Hot Forged valves are then trimmed through the automatic trimming machine to remove the extra flashes and material. Then his material is cleaned through the automatic shot blasting machine to clean the surfaces and give a clean surface of the valves. These cleaned valves are then sent to the automated machining centre for the machining.
The Die-casted parts of the regulators are then trimmed through an automated machine for removal of the excessive material. These are then surface treated by the Automated 7 tank cleaning process and Powder coated with the desired colours through the Automatic Powder coating system. This powder coating is done to protect the zinc surface from oxidation and also for the surface finishing and aesthetics of the regulators.
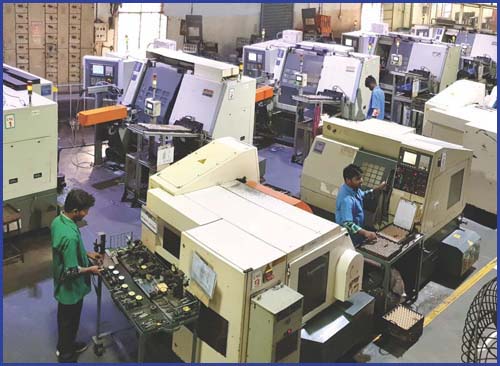
MACHING
The treated and cleaned valves are then machined for the various dimensions and technical requirements and functions of the valves through the Robotic CNC Machines. The Inlet, Outlet, Threading and other processes are done automatically by the robotic machines as per the specifications of the required product. They are also checked for the dimensions by the quality control inspectors at the machining centre. They are then once again cleaned and sent forward to the assembly and finishing of the valves.
The treated and cleaned regulator parts are then machined for the various dimensions and technical requirements and functions of the valves through the Automated Machines. The Inlet, Outlet and other processes are done automatically by the Automated machines as per the specifications of the required product. They are also checked for the dimensions by the quality control inspectors at the machining centre. They are then once again cleaned and sent forward to the assembly and finishing of the regulators.

ASSEMBLY
The Machined valves are then assembled with various other parts for the functioning of the valves. These other parts are fixed into the valves as per the requirements and then tested for their performance and working. Every piece is checked through automated test equipments.
The Machined regulator parts are then assembled with various other parts for the functioning of the regulators. These other parts are fixed into the regulators as per the requirements and then tested for their performance and working. Every piece is checked through automated test equipments.
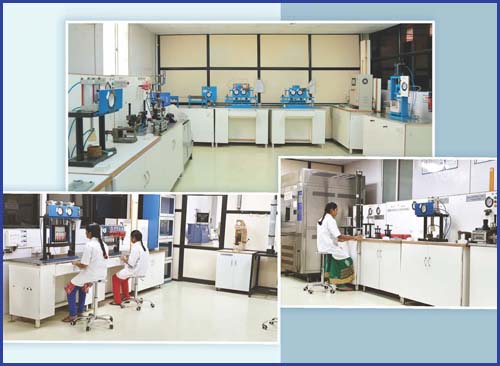
QUALITY CONTROL
The products are then packed as per the requirements and are being marked, labelled, sealed for the shipments and sent to the Finished Product Bay and Despatch Section.
These packaged materials are then despatched to the customers as per the despatch instructions received from the customers. The complete documentation and trackability of the production process are done and recorded.
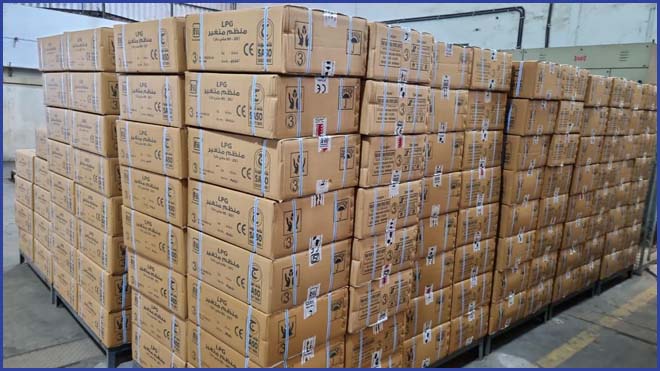
PACKING & SHIPMENT
TVL has global penetration for its state of the art commercial kitchen equipments range comprising of various products for Domestic & High Pressure segments.
Yes, we at TVL believe in VALUE ENGINEERING THROUGH QUALITY & the sale of 60 million units to satisfied customers all over the world for more than 3 decades, is itself a testimony of our capability, dedication and commitment.
The Raw Material is first Inspected for quality as per the standards and then taken for the processing.
For the Valves, Brass Rod is cut into desired size of billets on an automatic cutting machine. These billets and then fed through a conveyer to the Automatic Hot Forging Machine where the required type of valve is hot forged to the desired shape. They are then then left for cooling. This cooled material is sent for further process.
For the Regulators, Zinc alloy ingots are fed to the automatic Pressure Die-casting Machine. The hot molten material is automatically injected into the pressure die casting moulds to take the shape of the desired regulators. The machines cast the regulator in 2 parts called the Body & the cover (known as regulator parts). The automatic die casting machine processes the material and gives the desired moulded parts for further processing.
The Hot Forged valves are then trimmed through the automatic trimming machine to remove the extra flashes and material. Then his material is cleaned through the automatic shot blasting machine to clean the surfaces and give a clean surface of the valves. These cleaned valves are then sent to the automated machining centre for the machining.
The Die-casted parts of the regulators are then trimmed through an automated machine for removal of the excessive material. These are then surface treated by the Automated 7 tank cleaning process and Powder coated with the desired colours through the Automatic Powder coating system. This powder coating is done to protect the zinc surface from oxidation and also for the surface finishing and aesthetics of the regulators.
The treated and cleaned valves are then machined for the various dimensions and technical requirements and functions of the valves through the Robotic CNC Machines. The Inlet, Outlet, Threading and other processes are done automatically by the robotic machines as per the specifications of the required product. They are also checked for the dimensions by the quality control inspectors at the machining centre. They are then once again cleaned and sent forward to the assembly and finishing of the valves.
The treated and cleaned regulator parts are then machined for the various dimensions and technical requirements and functions of the valves through the Automated Machines. The Inlet, Outlet and other processes are done automatically by the Automated machines as per the specifications of the required product. They are also checked for the dimensions by the quality control inspectors at the machining centre. They are then once again cleaned and sent forward to the assembly and finishing of the regulators.
The Machined valves are then assembled with various other parts for the functioning of the valves. These other parts are fixed into the valves as per the requirements and then tested for their performance and working. Every piece is checked through automated test equipments.
The Machined regulator parts are then assembled with various other parts for the functioning of the regulators. These other parts are fixed into the regulators as per the requirements and then tested for their performance and working. Every piece is checked through automated test equipments.
The products are then packed as per the requirements and are being marked, labelled, sealed for the shipments and sent to the Finished Product Bay and Despatch Section.
These packaged materials are then despatched to the customers as per the despatch instructions received from the customers. The complete documentation and trackability of the production process are done and recorded.
TVL has global penetration for its state of the art commercial kitchen equipments range comprising of various products for Domestic & High Pressure segments.
Yes, we at TVL believe in VALUE ENGINEERING THROUGH QUALITY & the sale of 60 million units to satisfied customers all over the world for more than 3 decades, is itself a testimony of our capability, dedication and commitment.
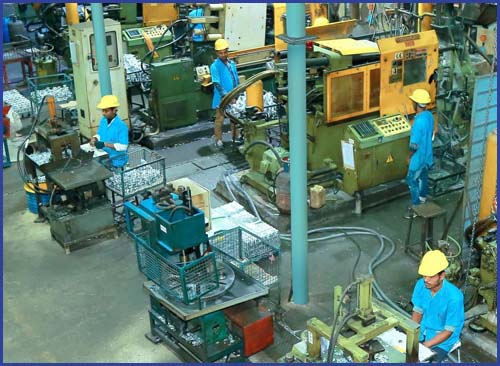
The Raw Material is first Inspected for quality as per the standards and then taken for the processing.
For the Valves, Brass Rod is cut into desired size of billets on an automatic cutting machine. These billets and then fed through a conveyer to the Automatic Hot Forging Machine where the required type of valve is hot forged to the desired shape. They are then then left for cooling. This cooled material is sent for further process.
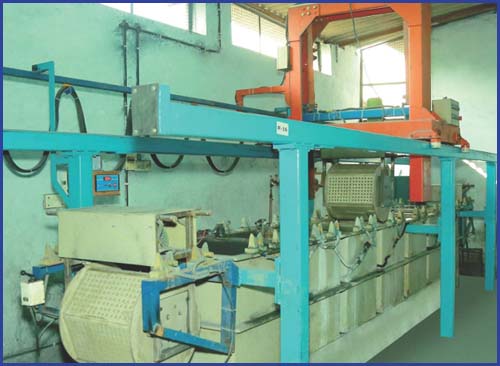
The Hot Forged valves are then trimmed through the automatic trimming machine to remove the extra flashes and material. Then his material is cleaned through the automatic shot blasting machine to clean the surfaces and give a clean surface of the valves. These cleaned valves are then sent to the automated machining centre for the machining.
The Die-casted parts of the regulators are then trimmed through an automated machine for removal of the excessive material. These are then surface treated by the Automated 7 tank cleaning process and Powder coated with the desired colours through the Automatic Powder coating system. This powder coating is done to protect the zinc surface from oxidation and also for the surface finishing and aesthetics of the regulators.
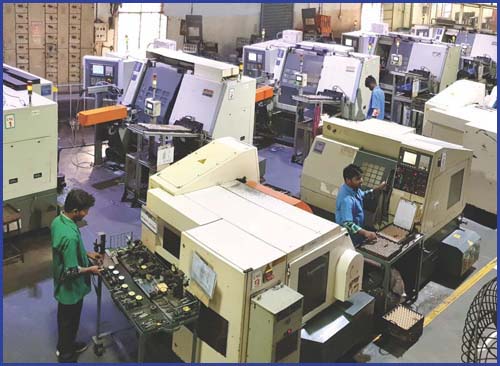
The treated and cleaned valves are then machined for the various dimensions and technical requirements and functions of the valves through the Robotic CNC Machines. The Inlet, Outlet, Threading and other processes are done automatically by the robotic machines as per the specifications of the required product. They are also checked for the dimensions by the quality control inspectors at the machining centre. They are then once again cleaned and sent forward to the assembly and finishing of the valves.
The treated and cleaned regulator parts are then machined for the various dimensions and technical requirements and functions of the valves through the Automated Machines. The Inlet, Outlet and other processes are done automatically by the Automated machines as per the specifications of the required product. They are also checked for the dimensions by the quality control inspectors at the machining centre. They are then once again cleaned and sent forward to the assembly and finishing of the regulators.
Quick Links
Products
Copyright © 2023 Transvalves India Pvt Ltd. All rights reserved.